|
|
HOME Technical Know-How Ceramic Manufacturing Process |
 |
 |
Refinement |
 |
1)
Cleaning: Wash with water soil stuck on the surface of a massive ore.
2) 수비 : When solid particles sink in the water, the particle size or specific gravity causes a difference in the sinking speed. Using such principle, elutriate particles in the material in the water and let water flow at a regular speed, making rough and heavy particles sink. This is a way of separating particles using the particle size and specific gravity, by letting flow fine and light particles in the suspension.
3) Sieving: In order to roughly identify particles in the material.
4) Separation: There are ways of separating by letting particles flow in the water or by the difference of magnetic power, or by making particles float and then capturing them. |
 |
Milling |
 |
During dry milling, byproducts cannot be made any smaller than a certain size because elementary particles get stuck to the wall or ball of the mill, forming a coating layer.
During wet milling, which is done by adding water to the material to make a slip, particles get scattered and cause no coating, which allows particles to be milled even finer.
Mills are largely divided into ball mills, hammer mills, and roller mills.
|
 |
Drying |
 |
Drying is a process in which water or other volatile compounds contained in a solid are removed by heat, reducing the content of such matters. Dried solid contains a little water. For instance, if material in the slip is dried using a spray dryer, the specific surface area for drying is increased by spraying and the material is forced to contact the heated dry air, instantly obtaining solid spherical particles. |
 |
Molding |
 |
1) Infusion Molding
A process in which slip is poured into the gypsum mold, then gypsum absorbs water from the slip, and the mold is removed while solids are kept in shape.
2) Extrusion Molding
The beauty of clay containing water lies in its plasticity. It is this property of clay that makes it possible to extrude a mixture of clay and water through a hole, make a plastic-clay column. Once cut into a reasonable length, the clay can be molded into any shape. The plastic-clay pillar has a consistent cross section and simple shapes, so it is widely used for molding circular or polygonal things with the center hollow or filled. It can be also used for making large pieces like clay pipes, carbon electrodes, insulators, or insulating tubes, protective tubes, and combustion tubes of thermocouples.
3) Press Molding
This method is used for molding tiles, special porcelains, and fire-resistant materials. Use only a small amount of plastic ingredients, or add wet powder, and pressurize with a plunger or a punch. With high productivity and a simple process, the method is the most commonly used.
4)
Injection Molding
A way of molding products with complicated shapes, unlike other methods, it requires a lot of organic binders for mixing, therefore binders get burned away in the process
5) Special Molding
* Rubber Press: Put ingredients in a rubber mold, mix it with oil or water, and add pressure to the liquid. It obtains a homogenous product because pressure gets evenly distributed.
* Hot Press: Unlike pre-exiting methods in which cooling, molding and sintering are to be done in order during the manufacturing of powder metallurgy and special ceramics, this method allows molding and sintering to be done simultaneously at high temperature. |
 |
Firing |
 |
Ceramic products are baked at high temperature in general, which is called firing. Though there are a few types of ceramic products, such as porcelains, fire-resistant matters, glass, gypsum, lime, carbon products, etc., the purpose of firing is largely divided into two as follows:
First, firing helps make products with a certain shape and strength by sintering ingredients. Second, firing causes a reaction of mixed ingredients, endowing them with appropriate properties or creating a desired compound. Major factors in firing that affect quality include chemical composition, mineral composition, particle distribution, packing density, volume density, firing temperature, firing time, cooling speed, and the atmosphere of firing. These factors are very important in the firing process for most ceramic products, and therefore require special attention. The firing process varies depending upon the composition and type of product and upon the purpose of firing. Since it is an extremely critical process, the manufacturer ought to have a full understanding of the selection and heating of kilns and ingredients.
* Sintering
The final stage of firing in which powder or compact get fused at a temperature below the melting point, turning into a condensed solid. Through sintering, powder particles becomes a porous massive with mechanical strength and for powder compact, as the volume shrinks, density, elasticity and tension increase and re-compression, re-crystallization, and the growth of crystals occur. |
 |
Manufacturing Process Flow Chart |
 |
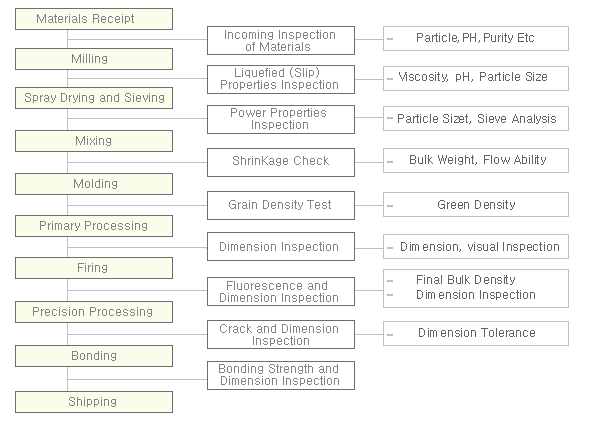
|
|
 |
 |
|